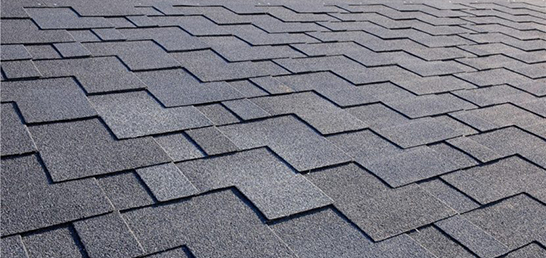
Someone once said that making a shingle was equivalent to mixing a refinery waste product with a little dirt and sprinkling it with rocks…and then, of course, giving it a lifetime warranty. If only it were that easy.
In reality, scientists and technicians spend countless hours in the lab trying to turn refinery bottoms into black gold.
The challenge in finding an asphalt that can withstand Mother Nature and meet the stringent requirements of shingle coating has become increasingly difficult. Historically good crudes for making roofing flux derived from Venezuela and Alaska’s North Slope are no longer available, and while Middle East crudes are still coming into the United States their impact is limited.
Long gone are the days when a refinery utilized a single crude source in its process. The crude blends used by most refineries these days are not only complex but constantly changing based on the political and economic environments, as well as the refinery’s processing capability. Many refineries receive their crude via pipeline, and while generally, they know what the complex makeup of that stream is, it is always changing and subsequently producing asphalt that can have a varied chemical makeup.
More recently shale oil has changed the oil landscape globally. The shale oil crude found in America, which provides more energy independence and supports the fuels markets well, produces much less asphalt in yield and the quality is less than optimal for the production of roofing coating when compared to historic asphalts. Examples of these shale oil crudes are Bakken, Permian Basin, Eagle Ford, Utica and Marcellus Shale.
So how do we work with these materials to support a strong asphalt shingle market and develop an asphalt coating that will stand the test of time and meet all the performance requirements? Most people outside of our industry have no idea how much chemistry and engineering goes into developing a quality asphalt roofing material.
Basic chemistry
It all starts with the basic chemistry of an asphalt, most commonly known as the SARA fractions: saturates, aromatics, resins and asphaltenes. What do these fractions look like? How much of each do we have? How can we manipulate them to make a better product? What are the expectations for the product? The answer used to be pretty simple. A shingle should shed water such that the home is kept dry. It should perform in both hot and cold climates and the coating should not flow in the summer, nor crack in the winter. And it should perform year after year, through all the different weather cycles, in all the different climates.
In more recent years we have been asked for increased performance to include algae resistance, elimination of staining, and impact resistance as the prevalence of hailstorms has statistically increased. These expectations become more important as a way to showcase the product against newly competitive roof coverings. How do we prove the formulations of the materials we have are superior in performance?
We showcase our laboratories that have also evolved. Asphalt laboratory testing has advanced over time to meet the qualities demanded from the roofing plant to the shingle industry. We used to define asphalt coatings only by physical property measurements – softening point, penetration and viscosity. This testing, while historically workable, does not speak to the overall performance of the coating or how it will perform in a shingle. Today, we must ensure the coating performs in every climate. Therefore, through the evolution of rheology, we determine how this material performs under different environmental conditions encompassing the natural stresses and strains of the world. From simple softening point and penetration testing from days past to viscosity and rheological measurements obtained from DSRs (dynamic shear rheometers) and BBRs (bending beam rheometers) used today, we incorporate all the technology to study and measure how asphalt reacts to all the conditions it will encounter as it performs in a shingle.
Once you have formulated the coating you must ensure that it blends well with the other chemistries in the shingle. This is no trivial undertaking due to the unique differences of the fiberglass mat, mineral fillers, granules and polymers that are available. The compatibility of the asphalt coating with all the other materials needed to make a shingle is an absolute must.
Remember that the asphalt shingle coating chemist needs to provide a unique formula for every plant they support as the raw materials are all unique to a geographic area. And once you think you have it solved, some variable changes, requiring you to go back to the drawing board.
Additives
There are numerous polymers, additives and recycled materials that can successfully be added to asphalt. Scientists utilize some of the most sophisticated laboratory equipment and techniques daily to monitor and design asphalt and finished products for our roofing shingles. The ultimate goal is determining how to add these materials in an economical manner and guarantee that they will perform to the consumer’s expectations for the next 20+ years.
Let’s start with the oxidation of asphalt, a standard process for producing asphalt used in a steep slope roofing shingle. Asphalt scientists have incorporated materials such as polyphosphoric acid (PPA), FeCl3, chemical modifiers, and a variety of both engineered and recycled oils to enhance or aid this process in an effort to utilize asphalts from the ever-changing marketplace. When investigating the use of these products one must consider not only the quality of the finished product but also any infrastructure additions that may be needed, environmental concerns, and cost to the consumer.
Another option is the integration of polymers as a method to produce a superior asphalt coating with enhanced rheological properties. But can polymers be added to every asphalt in the same way? The simple answer is no. Not every polymer works with every asphalt, so there is work to be done to find that perfect formula that meets the quality requirements at an economical price. Again, the science here is critical as things like mixing, temperature, transportation, and the shelf life of the material can all have an impact on the final product.
Recycling
If you thought the addition of polymers was challenging, let’s add the use of recycled polymers from materials like milk jugs and old tires. How do you manage the quality of those materials before adding them to your process? Next, consider the idea of cradle-to-cradle when that shingle has fully served its purpose and is ready to be replaced. We need to think about how to keep these shingles out of the landfill and reclaim them back to use – in roads, roofing or other applications.
In today’s environment, our challenge is to utilize the constantly changing product being made by the refinery along with additives, modifiers and recycled materials to enhance the finished product and meet the increasing demands of sustainable materials management, all while maintaining superior quality and performance along with that lifetime warranty.
As the asphalt quality produced by refineries continues to evolve, roofing companies have been challenged to upgrade their infrastructure, improve their oxidation processes and add new technologies to compete with and participate in the green environmental wave of legislation and regulations. Add to that a new generation of customer expectations and it is easy to see that these are the challenges of today and the future and the chemists in the asphalt roofing industry are actively engaged in studies to find solutions.
Michael Franzen, Ann Hamer and Laurand Lewandowski collaborated on this article.