Innovations for a challenging location
I have given hundreds of presentations in my years as an Asphalt Institute Regional Engineer. A phrase that I have used an untold number of times as part of those presentations is, “we are an industry of inertia.”
I don’t say it as a compliment. Rather, I am communicating that we tend to slowly move toward new technology or new ways of doing things. This is not necessarily a bad thing as the consequences of adopting unproven materials or techniques could be catastrophic if they prove themselves to be poorer performers than current technology. On the other hand, forward progress to better and better-performing roads cannot be achieved without trying new ideas. It’s a real quandary.
Inertia can be defined as, “a tendency to do nothing or to remain unchanged.” Not exactly a term that many would appreciate being associated with. Or more formally, as many of us learned in physics, “a property of matter by which it continues in its existing state of rest or uniform motion in a straight line unless that state is changed by an external force.” While not too much better, I find encouragement in that last clause, “unless that state is changed by an external force.” This means that we are not obligated to the same path we have always trodden. We can do things differently or try new technologies or ideas if we are willing to calculate the risks and boldly explore their potential to improve pavement performance.
The “external force” that is needed in the world of pavements is a person or people. These people choose not to ignore the lessons of the past, but rightly believe that other options can and should be explored with the goal of enhancing the performance of future pavements. One such individual is State Asphalt Engineer for Utah, Howard Anderson.
Anderson, along with Region 2 Materials Engineer Lonnie Merchant, determined to try something radically new for Utah and much of the paving world. They came to the conclusion that a highly modified Superpave mixture could be successfully installed in a single thick lift. Moreover, they also concluded that changes to the mix design criteria would be needed to produce a good design which could be constructed without major changes by whoever was the successful bidder for the project. And then they got bold when Merchant chose a test location that exposes the mix to very challenging physical loading and environmental conditions.
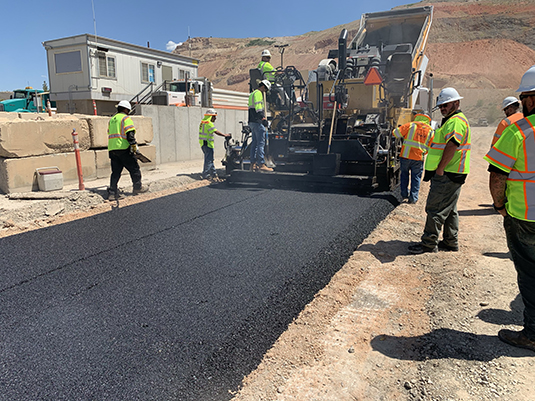
Calculating the risk
Thinking that you have a good idea that should be tried in the field and running out and implementing this idea is a fool’s risk. While it is true that this approach could work out, it is at least as likely that it will not. Far more prudent is to do background work on the idea before heading to the field.
In the case of a highly modified asphalt mixture that is installed in a thick, single lift, the Utah Department of Transportation (UDOT) was not about to play the fool’s hand. They wisely looked at what had been done by others, what they had done in the past and laboratory testing of their own. Armed with this information they proceeded to set up a specification for the installation of this technology on a UDOT project.
What others have done
The most recent installation of thick asphalt lifts by a DOT was in South Carolina for applications along their eastern seaboard. This is a very popular tourist destination and rehabilitation time was seen as a valuable consideration in addressing pavement needs.
By constructing in a single 5-inch lift, they would reduce construction time and speed a return to service. Moreover, South Carolina was armed with the results of research that they had sponsored on the National Center for Asphalt Technology (NCAT) at Auburn University which was very favorable. Construction data for this installation indicates that it was built to a compacted depth of 7.9 inches with consistent densities of about 95 percent of theoretical maximum density throughout its depth.
Also, in a previous cycle on the NCAT test track, an industry-sponsored section which was highly modified and built in a single 5.75-inch compacted lift performed very well. The recorded performance for this installation was excellent when evaluated in terms of typical field performance standards.
Utah’s experience with highly modified asphalt
Over five years ago, the mixture lab for UDOT fabricated several Hamburg Wheel Tracking specimens in incrementally richer dosages of highly modified binder in a typical Utah 12.5-mm Superpave mixture all the way up to 6.8 percent binder. These increasing binder contents effectively closed down the air voids. No failing test results were seen after 20,000 passes. To further stress the specimens, the lab took the 6.8 percent specimens and ran them a second time on the Hamburg increasing the mass by 20 additional pounds to each wheel. Even then, after 40,000 passes, half with the additional loading, the specimens passed the 10 mm maximum rut depth criteria.
Encouraged by these laboratory results, Utah successfully installed two sections with highly modified binders about four years ago – both were on state routes of modest volumes. On both projects, the highly modified binder was substituted for the respective mix design binders with no further changes to the design. Moreover, these installations used standard construction techniques and lift thicknesses. UDOT learned quite a bit from these jobs further encouraging them to construct more field projects.
Anderson was further convinced from these experiences that a much thicker compacted mat thickness could be achieved with relative ease. If so, then he envisioned a faster construction process that also eliminates the problems commonly associated with multi-lift paving. Namely, tack coat and delamination between layers. There is no opportunity for delamination with a single lift. As Anderson stated, “I’ve always wanted to find a way to do this (a single thick lift). It seems a waste of time to pave the pavement twice.”
Anderson was also convinced that he could specify a higher minimum density requirement for highly modified mixes. UDOT uses percent within limits (PWL) with an already stringent lower specification limit. After careful consideration, a target density of 96 percent for the top three inches was specified for highly modified asphalt mixtures with the lower spec limit to be set at 94.0 percent.
Time to test
As the external force to overcome the inertia of the past and to prove wrong those that say that it can’t be done, Anderson and Merchant were certain that an installation of a highly modified bound mix, placed in a single lift, could be successfully done. In the end, it was Merchant that chose the location, and he picked a doozy. Namely, the port of entry for eastbound Interstate 80 trucks at Wendover, Utah.
I-80 is a major east-west trucking route moving goods from west coast ports to the Midwest and beyond. This location has an AADT (annual average daily traffic) of about 7,600 vehicles per day, but over half of the daily vehicles are trucks. Therefore, the location has thousands of trucks loading materials every day. Moreover, the test installation is on both sides of the scale. So, there will be many trucks either moving slowly or at a complete stop after braking to reduce travel speeds to get weighed and then accelerating to return to the highway.
Environmentally, this location is also very hot in the summer months. A hot pavement carrying heavily loaded trucks that are moving slowly or stopped is the perfect recipe for rutting. Yes, a brutal location, but as Merchant said, “If it works here, it’ll work anywhere.” Approximately 330 tons of mix were needed to complete the project.
Project special provisions
The uniqueness of the mixture and UDOT’s field and lab experience warranted changes to the standard Superpave specifications. A 12.5-mm nominal maximum Superpave mixture using a PG 76-34 binder was specified for the project. According to LTTPBind, a PG 64-28 would be the typical binder for this location. Recognizing that typical mix design criteria would not be wise, alterations were made as shown in Table 1. Also in Table 1 are the mix design values as submitted by Staker-Parson, the successful contractor for the project. Staker added Evotherm 3G to the mixture as a compaction aid because of their positive experience with the product.
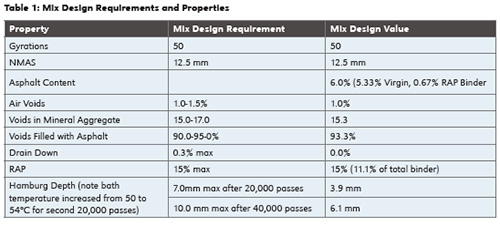
Test strip construction
A test strip for this mixture was constructed by Staker- Parson’s Beck Street facility north of Salt Lake City where it was produced on June 2, 2021 (Figure 1). While this was a wise choice, there were some notable differences at this location compared to the Wendover test site.
First, for the test strip, there is virtually no haul, while it is just over two hours to Wendover. Second, the test strip site is a gravel material, while the Wendover site is milled PPC pavement with confinement on both sides. Thus, the test strip site was likely a harder place to get proper densification. Despite these differences, excellent density was achieved without any dramatic changes from Staker’s typical compaction process.
It is worth noting, when the breakdown roller was working the unconfined edges, great stability was found in this material even at over 290°F. To no one’s surprise, there was some education that needed to occur to get an adequate feed for such a thick ribbon. No significant issues were encountered constructing the test strip.
Constructing the test site
The day following the construction of the test strip, Staker-Parson was ready to install the highly modified asphalt mixture at the Wendover test site (Figure 2). Early that morning, trucks were loaded and headed across the state to the Nevada border. The mixture was deposited in a large windrow alongside the milled concrete. A material transfer vehicle (MTV) picked it up and placed it into the hopper of a paver. Slowly and steadily, each side of the port of entry was paved. There was a delivery hiccup that delayed one truck that resulted in a slight dip, but construction progressed mostly without any hitches.
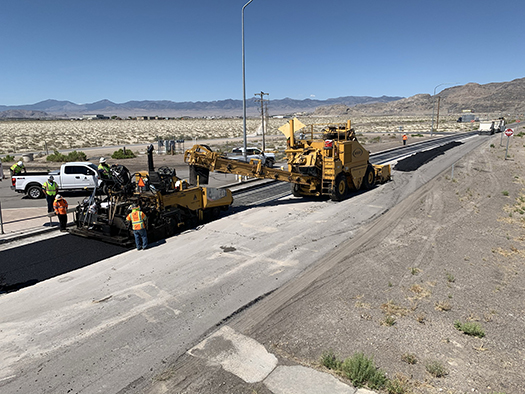
The mix arrived at the job site at an adequate temperature, about 275°F, even after the long haul. Breakdown compaction was done via two Hamm HD 140i compactors. Densification was achieved with a standard rolling pattern of five passes over each location on the mat. Finish rolling was accomplished merely for final appearance.
Densities were measured using six-inch cores. The density requirement of 96 percent of theoretical maximum density in the specifications applies to the top three inches alone, but the cores were sliced into a top and bottom half. Both halves were tested. The results of that testing are seen in Table 2 below.
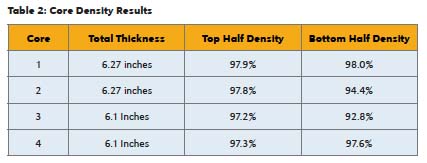
Early performance
Caution was exercised to allow for the reopening to traffic. First, the thickness meant that cooling took some time. Moreover, it was deemed prudent to give the material plenty of time to fully set up before allowing traffic on it. Construction was completed on a Thursday, but traffic was held off until Sunday afternoon, or for three days. Future similar installations are not expected to have as much of a delay before opening to traffic.
To date, no negative issues have occurred under traffic. Performance has been outstanding, as can be seen in the picture above (Figure 3). This image was taken more than two months into its service during which time it had already been exposed to at least 17 days where the air temperature was 100°F or more. Moreover, if typical traffic volumes have occurred, then over 230,000 trucks have already driven on the experimental site. Everyone involved with this project is ecstatic at the early performance.
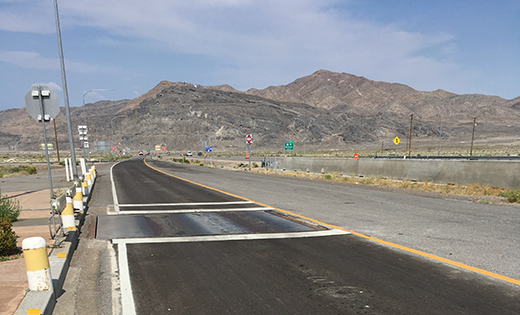
Future projects
Additional highly modified projects are being considered for the other end of the spectrum – thin lift overlays, because of the performance of both this installation as well as the other previous projects. Other thick, single lift project locations will also happen. No worthy candidates have currently been identified.
Anderson is hoping to try this technology on applications that are often constructed with concrete pavement. The speed with which a pavement can be closed, repaired/constructed and reopened to traffic is very attractive. For a project like the size of this one, 48 hours or less may be reasonable.
At least in Utah, industry movement has been altered and the results are very encouraging.
Johnson is an Asphalt Institute Regional Engineer based in Montana.
Howard Anderson, P.E. contributed to this article.