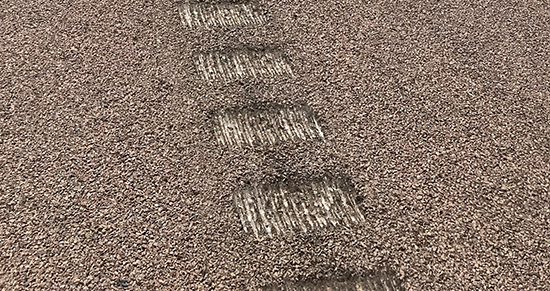
Through the course of conducting my duties for the Asphalt Institute, I have increasingly noticed the use of centerline rumble strips when traveling. I could not help but wonder what, if any, negative effect they might be having on pavement deterioration.
My concern stemmed from the fact that the final longitudinal joint on many rural two-way roadways is at their centerline. So, milling a rumble strip into what is also commonly the most problematic location of a pavement raised concerns for me.
That quickly evolved into a desire to make information available on the best ways to install and maintain all rumble strips, especially at the centerline.
Background
The use of rumble strips on roadways is practically expected by today’s drivers. But that hasn’t always been the case. The need for passive restraints was increasingly recognized by highway engineers as traffic numbers increased following World War II.
“Popular Mechanics” magazine reported in their February 1953 issue that a “singing” highway in New Jersey had been installed the previous year. This was the 165-mile Garden State Parkway which included 3-foot corrugated concrete shoulders designed to alert drivers that wandered out of their lane. This is widely considered to be the first use of rumble strips.
While the corrugations were only on the shoulders, it was also reported that centerline installations were also occurring on rural two-lane highways in the same 1953 article. Thus, centerline rumble strips appear to have been used since this same time, albeit to a far lesser extent than their shoulder cousins.
From the time of these initial installations in the early 1950s until the mid to late 1980s, only scattered use of rumble strips was found in the literature. While they were being used, they do not appear to have been very widespread. From the late 1980s through the early 2000s, a large number of reports were found indicating a notable increase in rumble strip usage around the U.S. and worldwide. Today they are commonplace.
Design of rumble strips
The Federal Highway Administration (FHWA) has established a formal process to determine if rumble strips are warranted on a particular facility. It is not the intent of this article to offer guidance on the decision to use rumble strips or not.
Rather, this article is designed to guide the reader on how to properly install rumble strips to maximize their effectiveness and to minimize any negative effects that they may have on pavement life.
Rumble strips fall into four categories: milled, rolled, formed and raised. This article will focus on the milled rumble strips as they are the most common category used in the United States and can present the greatest potential for negatively affecting long-term pavement performance.
Key 1
Selecting a good candidate pavement
The most important factor in predicting the effect of rumble strips on a pavement’s performance is the pavement’s current condition. It is very important to pick a pavement that is in fair to excellent condition when initiating a design of a rumble strip section.
Data indicates that when a pavement is in fair or better condition, rumble strip installation has minimal negative impact, perhaps unnoticeable, to the pavement’s life. On the other hand, for a pavement that is not in such good shape, the impact on pavement performance has been found to be notable.
The best time for rumble strip installation is shortly following the construction of a fresh asphalt surface. Many agencies have developed systematic policies that have rumble strips installed on all new, overlaid or reconstructed pavements. This not only ensures the best quality pavement possible, but it also maximizes the time before an overlay or other maintenance operation will occur that could reduce the effectiveness of rumble strips.
But candidates are not limited to new pavements. It is acceptable to consider rumble strips on pavements that are in the fair or better condition. On a deterioration curve such as the one shown, or from within a pavement management system, an agency is encouraged to establish a threshold value that creates a “go” or “no go” decision, unless safety warrants their usage on a poorer pavement. Some agencies have adopted policies that set a maximum age or minimum thickness to attempt to avoid negative ramifications of rumble strip installations.
As high-quality pavements are the most desirable, constructing such pavements is the best way to have good candidates for rumble strips. While it is vital across the entire width of the pavement, paying close attention to any longitudinal joints is extremely important. The Asphalt Institute has many resources available on longitudinal joints at asphaltinstitute.org.
Some key takeaways from the information on longitudinal joints are as follows. Plan for their construction, minimize longitudinal joints, especially on the top lift. Use echelon paving whenever possible to eliminate cold joints. Pave straight on the first pull to make it easier to get proper overlap on subsequent pulls. Strive to maximize the density of the joint using recommended practices. And finally, consider using technology to improve the density or reduce the permeability at the joint.
One technology that can be used to improve the density of the joint is longitudinal joint heaters. The joint heaters available for use today are far more advanced than their older versions. They heat the existing materials, but without too much to damage the asphalt.
Intelligent compaction and pneumatic rollers both have been shown to assist in getting the most density possible at the joint. Lastly, advancements in technology now offer the option of using specialized materials designed to improve the joint. These include longitudinal joint sealants, also known as void-reducing asphalt membranes, which are applied to the surface before new material is laid, or surface sealants that are applied after finish rolling.
Regarding the planning of longitudinal joint location, consideration of rumble strips is wise. Namely, purposefully keeping rumble strips at least a few inches away from the joint helps to assure that they are not placed in what is potentially the most vulnerable location in the pavement.
It is noteworthy that having the rumble strips near the vehicles helps to keep them clean and dry. This is a result of the wind generated by the vehicles helping to accomplish this. Shoulder rumble strips are more in need of this consideration as those at centerlines are inherently near traffic.
Perhaps the most controversial topic related to rumble strips is the question of whether to seal them or not at the time of construction. In 2016, NCHRP Synthesis 490 reported that only 44 percent of responding agencies use a sealant as part of rumble strip construction, but fully one-third of those reported that this is not a standard practice.
Understandably, the assurance of proper sealing of the surface was the main rationale for sealant applications. The most common means of sealing rumble strips is with a fog seal. Sealing rumble strips is a wise choice as it is a cost-effective insurance policy for your pavements. Moreover, if rumble strips are deemed necessary on a roadway that is in fair or worse condition, sealing these installations should not be skipped.
Key 2
Constructing high-quality rumble strips
High-quality rumble strips are those that are cleanly cut and milled into the asphalt surface. Well-maintained milling equipment will cut better into the asphalt, minimizing the potential to tear the material.
Cleanly cut asphalt will inherently be less permeable than asphalt that tears while being milled. Therefore, use good milling practices – systematically checking the teeth on the milling head for wear and replacing those that are worn according to the equipment manufacturer’s recommendations and using water to assist with the milling operations.
Key 3
Maintaining rumble strips
The maintenance of rumble strips is not commonly considered independent of the rest of the roadway. In fact, NCHRP Synthesis 490 reported that only five agencies stated that they purposefully reseal rumble strips.
Typically, maintenance operations are planned and scheduled for a given route. If those routes have rumble strips, then the effect of the maintenance treatment on their performance should be considered. Namely, does this maintenance treatment reduce the noise produced by the rumble strip when they are encountered by drivers? If the answer is yes, and it is of sufficient magnitude, then readdressing the rumble strip may be warranted.
For example, while chip sealing a pavement will undoubtedly quiet existing rumble strips, it is usually not enough to raise concerns as rumble strips still provide their intended function of alerting wandering drivers. On the other hand, if an ultra-thin overlay or perhaps a micro-surfacing treatment is being applied then existing rumble strips are effectively eliminated. In this case, re-cutting rumble strips is needed to reestablish their functionality.
Traveler safety is the primary driver for rumble strips
Cutting into a pavement always raises the question of the effect that it will have on the pavement. When it comes to rumble strips, this is a secondary concern as improving safety for the traveling public is the primary concern. As such any loss of life of the pavement is easily worth it if human lives are saved. The data for rumble strips overwhelmingly shows that they are very effective in reducing run-off-the-road and head-on accidents. They simply save lives.
The very good news is that when rumble strips are a part of a systematic implementation on new, overlaid or reconstructed asphalt pavements, their negative effects on the pavement are limited. The more deteriorated the pavement is when rumble strips are actually installed, the faster the deterioration. So, every effort should be made to avoid installing rumble strips on deteriorated roadways that are in less than fair condition.
We can help keep travelers safe and keep our asphalt in good shape if we consider them both when it comes to rumble strips.
Johnson is an Asphalt Institute Senior Regional Engineer based in Montana.
More information
If you are interested in learning more about the physical design of rumble strips or a decision support guide consider these resources for further information: safety.fhwa.dot.gov/roadway_dept/pavement/rumble_strips/, “NCHRP Synthesis 490: Practice of Rumble Strips and Rumble Stripes” and “NCHRP Report 641: Guidance for the Design and Application of Shoulder and Centerline Rumble Strips.”