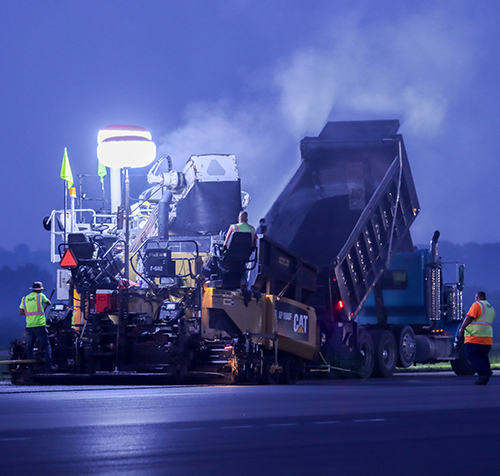
Located among world-renowned horse farms and situated directly across from Keeneland Racecourse, Blue Grass Airport (LEX) in Lexington, Kentucky is the primary commercial service airport for central and eastern Kentucky.
More than 1.4 million passengers depart or arrive annually at LEX via four major airlines: Allegiant, American, Delta and United. LEX also provides military, general aviation, charter and air cargo services.
With only one major runway (RW) large enough to accommodate commercial aircraft, any repair and maintenance work on the RW must be done at night generally between the hours of 12:30 a.m. and 5:00 a.m. when there are no scheduled flights.
The last resurfacing of the 7,004-ft long by 150-ft wide RW and associated taxiways (TWs) was performed in August 2006. Since then, crack sealing has only been accomplished twice and no patching has been needed. But with the RW surface being 15 years old and the unyielding Federal Aviation Administration (FAA) requirement of having no Foreign Object Debris (FOD) as a result of cracking and raveling, it was time for a new surface.
Scope
The project required mill and overlay of all of RW 4-22, the southern half of TW A and six connector TWs. Other project elements included widening one connector TW, making drainage and electrical improvements including lighting and adding temporary and permanent pavement markings.
A mandatory pre-bid conference was held along with site visits for potential bidders prior to bid opening on July 8, 2020. The pre-bid conference was intended to help clarify and explain required construction methods, procedures and safety measures. The construction contract was awarded on July 29, 2020.
There were four phases in the project. Construction hours for Phases 1, 3 and 4 were established between 12:30 a.m. and 5:00 a.m.
Phase 2 however, which involved a variable depth precision mill for minor grade corrections and a uniform 3-inch overlay for all RW 4-22, had to be accomplished during a scheduled 72-hour airport closure from 6:00 p.m. Thursday, Aug 19 to 6:00 p.m. Sunday, Aug 22, 2021. No fixed-wing operations were allowed during this well-planned closure. Liquidated damages in the contract were $3,000 per every 30 minutes beyond the allowed construction times for all phases.
An unexpected opportunity
The Lexington-Fayette Urban County Airport Board awarded the competitively bid construction contract for $16.2 million to ATS Construction LLC, a large roadway and construction contractor that operates in and around Lexington, Kentucky. Their sister company, The Allen Company, served as a major paving subcontractor on the project.
According to Mark Day, Director of Development and Facilities at LEX, the cost for project planning, design and construction administration totaled just over four million dollars. HDR was the primary design firm, with Tim Ward serving as Project Manager and Anthony Pellegrino serving as the Resident Project Representative (RPR) during construction. S&ME performed the quality assurance or agency acceptance testing, while ATS performed their own quality control testing. Both S&ME and ATS labs are AASHTO accredited. Several other specialty consultants were also involved.
During the pre-construction meeting held in September 2020, Mark Day reflected that “It was clear that we had experienced leadership from the contractor, the design and construction administration team and the airport. All parties were eager to take advantage of COVID-related impacts to funding and staff workloads occurring in both the aviation and construction industries.”
Specifically, Day was referring to the team seizing the opportunity to get a jump on Phase 2 by milling and overlaying in the Fall of 2020 approximately 4,500 feet of Taxiway A and associated ladder TWs rather than during the 72-hour closure scheduled for August 2021. Day said advancing this portion of the work provided multiple benefits for all parties:
• Minimized impact to the airlines and passengers with lower levels of air traffic during COVID restrictions.
• Reduced pressure off the 72-hour paving window by reducing the volume of material milled, produced, placed, tested, etc.
• Served as a trial run for all parties to work together on the airfield under less stringent conditions.
Keith Bishop, Quality Control Manager for ATS, is no stranger to airfield paving, the FAA’s P-401 specification and its use of Percent Within Limits (PWL). This was his fourth airfield project. He commented that the pre-con meeting placed a large emphasis on FOD, “totally different than normal paving jobs.”
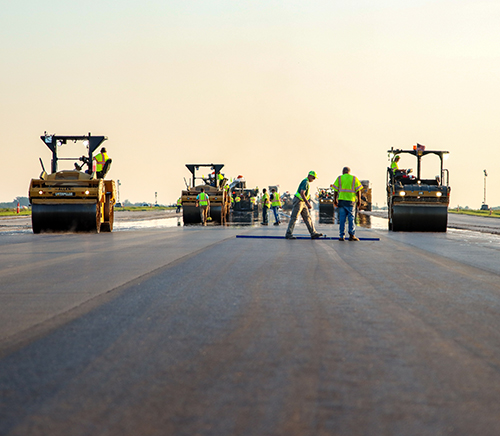
The mix
For the single three-inch surface lift, the project specifications required Gradation 1 in the FAA’s P-401, a 19mm (3/4”) nominal maximum aggregate size (NMAS) dense-graded mix.
According to Bishop, ATS designed the mix to stay as fine as possible within the required gradation band. “It really acts more like a 12.5mm mix and leaves a nice tight texture on the surface. We have had great results over the years using similar mixes.” The aggregate gradation is shown below, with 98 percent passing the 19mm and 88 percent passing the 12.5mm sieves.
The blend was 90 percent crushed limestone and 10 percent natural sand. No RAP was allowed. This contributed to a very low dust content in the mix with the dust to effective binder content at 0.8. VMA was 15.2 percent during mix design (14 percent is the required minimum for P-401 Gradation 1) and stayed above 14.5 percent during production. This high VMA resulted in a relatively high 5.4 percent binder content at the designed 3.5 percent air voids. The binder was a PG 76-22 modified with SBS and supplied by Phillips 66. An SS-1H emulsion was used for tack coat.
Todd McDaniel, Project Manager for ATS, stated there was a control strip placed in the fall (prior to paving TW A) and another control strip this spring. “What we learned in the fall was the roll down was significantly less than our normal mixes. Normally we see 1/4” roll down per inch of uncompacted mat, but with this mix we were closer to 1/8”. So, to get 3” compacted, we were placing closer to 3 ¼” to 3 ½”.”
Per the P-401 specification, the test strips included a longitudinal cold joint. “We tried different things but got the best results by mounting a ‘pizza wheel’ onto a roller and cutting when the mix had cooled to around 160 degrees F. This left a nice clean edge to pave against with the next pass and was easier to keep straight,” added McDaniel.
72-hour closure
Day was confident leading up to the pressure-packed weekend: “Advanced planning and contingency measures have been so thorough, that I found myself relaxed going into one of the most critical rehabilitation projects this airport will experience. As LEX only has one commercial service runway, it was essential to keep this runway pavement in great shape for the traveling public.”
The 72-hour closure was roughly split into thirds: one day to mill the entire RW, one day for paving and one day to allow the new mat to cool and to place the markings. Once the milling started, all paving and markings had to be completed before the RW could be reopened to aircraft. FAA safety rules do not allow jet aircraft to operate on milled surfaces due to FOD concerns. This meant that weather delays would result in an extension of the runway closure beyond Sunday at 6:00 p.m., along with the cancellation of commercial flights.
The forecast leading up to the weekend was not promising, and it rained several inches on Wednesday and Thursday. But the skies cleared just prior to 6:00 p.m. Thursday when the milling operation started and there was no rain for the entire closure.
Equipment included:
• 8 milling machines operating at one time
• 3 dedicated local plants producing the same mix
• 60 trucks utilized to haul millings and deliver 800 loads of hot mix
• 4 paving trains running concurrently; two by ATS and two by The Allen Company
• 4 Material Transfer Vehicles (MTV), each in front and feeding a paver
• 4 pavers, each laying 15’ wide lanes for all passes
•12 total rollers, 3 behind each paver compacting the mat
ATS crews paved one side of the centerline while The Allen Company paved the other side. The four paving trains started in echelon running down the centerline for the entire RW length. Then ATS’s two trains paved in echelon on one side while The Allen Company’s two trains paved in echelon on the other side.
No transverse construction joints were ever required. Longitudinal joints were cut back at 30’ and 60’ from centerline on both sides, resulting in only four cold joints across the entire 150’ wide RW.
“From an engineering standpoint, paving the entire runway in a 24-hour window will result in longer useful life of this pavement. Reducing thousands of feet of transverse joints and utilizing more hot joints will save significant maintenance dollars over the next decade,” said Day.
Per the specification, grooving on the RW will not occur until the new pavement has been down for at least 30 days to allow the binder to stiffen on the surface.
Job well done
Dedicated team members and outstanding planning and coordination led to a successful runway resurfacing. The runway was closed at 6:30 p.m. Thursday and the first plane landed on the new surface at 6:05 p.m. Sunday.
Buncher is the Asphalt Institute Director of Engineering.