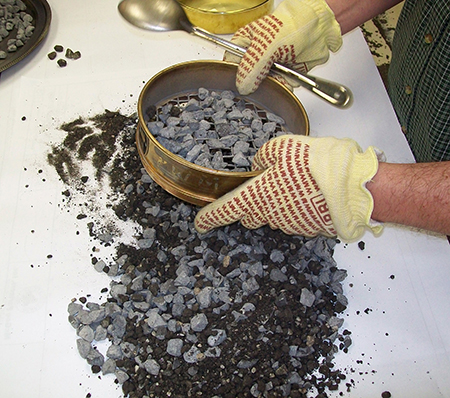
Adopting a 60:40 Correct Optimum Asphalt Content appears to improve roadways
By Bob Horan, P.E.
The use of Reclaimed Asphalt Pavement (RAP) tops the list of recycled products being used in the United States. An estimated 82.2 million tons of RAP were used in asphalt mixtures in 2018 in the United States according to a survey by the National Asphalt Pavement Association (NAPA).
Georgia Department of Transportation (GDOT) recycled an estimated 1.4 million tons of RAP into new asphalt mixtures in 2018. That same report stated that the average percentage of RAP used in 2018 was about 21 percent nationwide from a state-by-state perspective. Georgia Department of Transportation (GDOT) reported that their average RAP percentage used in asphalt mixtures was 25 percent.
GDOT specifications (Section 402 Recycled Asphaltic Concrete) allow up to 25 percent RAP when a batch plant is being used and up to 40 percent when a drum plant is being used regardless of whether the mix is a surface, intermediate or base mix.
Because RAP is comprised of asphalt binder and aggregate, the addition of RAP into new asphalt mixtures reduces the amount of virgin asphalt binders and aggregate needed in the mixtures. It is estimated that the use of RAP has reduced virgin binder usage by 4.1 million tons (23 million barrels) and replaced 78 million tons of virgin aggregate in a single year.
Performance concerns
While Georgia DOT recognizes the benefits of the use of RAP in keeping the cost of paving down and conserving natural resources, they also have a responsibility to the public to make sure asphalt pavements being constructed perform well for the expected service life regardless of the amount of recycled materials used.
GDOT began to observe performance-related problems with high RAP (25% or higher) asphalt pavements using conventional mix design practices. These issues included a dry appearance and premature aging in the in-place mix as well as increased segregation and coarse streaking in the mixture during construction. GDOT was also looking at pavement evaluation data that indicated that pavement repair and maintenance was needed earlier than expected on high RAP sections.
Based on observations of early deterioration of high RAP pavements, GDOT was concerned about how the addition of high percentages of RAP was impacting long-term performance of asphalt mixtures. GDOT started a research effort in 2012 to evaluate the impacts of high RAP contents on performance, to evaluate the amount of RAP and virgin binder blending and to identify ways to improve the performance of high RAP mixtures.
The question was why are these performance issues occurring in high RAP content mixes? Something that stood out to GDOT experts was the presence of low total binder contents and binder consisting of higher percentages of aged RAP binder in the mixtures.
“The adoption of Superpave volumetric-based mix design method that tended to reduce the total binder content (especially for higher volume roadways) and the decision to allow increased percentages of RAP which increased the binder replacement percentage from the RAP seem to be major factors in our observation of less durable asphalt pavements,” said Sheila Hines, former GDOT State Asphalt Engineer.
“The original GDOT mix design called for 100 percent credit for RAP binder. As a result, the typical asphalt mixture had lower binder contents than historically seen and the percentage of aged binder versus virgin binder was increased,” said Hines.
Changes to mix design procedures
During their ongoing research effort, GDOT’s Office of Materials and Testing decided to start looking at other ways to address the reduced performance of RAP mixtures, without reducing the percentage of RAP that is allowed.
Changes were made to the mix design procedure which targeted increasing total binder content in the mix. These changes included specifying mixes with finer aggregate gradations, requiring a minimum film thickness based on aggregate surface area, reducing design gyrations (65 gyrations for all mixes) and specifying minimum binder contents based on mix type. In addition, GDOT started adopting performance tests related to rutting and permeability to the mix design protocol. GDOT’s research showed that these changes resulted in slightly higher binder contents in produced asphalt mixtures.
GDOT conducts research on RAP
GDOT also wanted to address the RAP itself and specifically what happens with RAP/virgin binder blending during production at the asphalt plant. Specifically, they wanted to know the extent that the aged binder from the RAP was actually available to coat virgin aggregate with the RAP binder and to be blended with virgin binder being added to the mix.
The concern (which is shared by many asphalt technologists) is whether RAP is essentially a “black rock” where the RAP binder does not separate from the RAP aggregate to any significant level. With this question in mind, GDOT conducted research to try to determine how much blending of the RAP binder with the virgin binder actually takes place in the asphalt plant. A second question was how much RAP binder actually coats the aggregate during the production of asphalt pavements containing RAP.
The research included work on experiments with both lab-produced and plant-produced mixes.
Black rock or blended RAP/virgin binder?
The pressing questions were: Is RAP really a “black rock” where the aged RAP binder does not come off the RAP particles during plant production so that it is available to be blended with the virgin binder being added to the produced mix? Or, does the RAP binder become completely free to blend with virgin binder being added during production?
The consensus among experts can be that the truth is somewhere in between no blending and total blending although current studies have not validated the exact percentage of blending that typically takes place. In almost all of the previous research, chemical extraction of the combined RAP/virgin binder was done to obtain samples that were tested for combined binder properties. Using this approach artificially ensures 100 percent blending – which is clearly not what happens during actual plant production.
GDOT tried to answer the black rock question with both laboratory testing and with actual plant production. For the lab tests, GDOT conducted tests to try to determine if the transfer of aged asphalt binder on the RAP particles was actually possible.
A lab study was done where non-preheated RAP was blended with virgin aggregate at production temperatures (350° F) with no additional binder being added in a pugmill mixer. Typically, RAP is preheated by many laboratories for asphalt mix design. GDOT does not preheat the RAP because it is not preheated in actual plant-produced mixtures. As shown in the image (above/below), no significant transfer of RAP binder to the heated virgin aggregate was observed or measured in the laboratory blending experiment.
To follow up with plant testing, GDOT partnered with Reeves Construction Company to conduct some testing by running 30 percent RAP with virgin aggregate through the contractor’s drum plant. The produced material was a combination of virgin aggregate and stockpiled RAP that was blended in a plant that was set up for regular plant production.
Samples of that material seemed to show some transfer of RAP materials to the virgin binders but upon closer inspection, the transferred material was not aged binder from the RAP but was actually fine RAP fines that brushed off easily. At the conclusion of the research, GDOT became believers in the black rock theory that entails the belief that very little, if any, blending with virgin binder occurs during production.
However, GDOT does acknowledge that there are some benefits to introducing black rock into the asphalt mixture. RAP aggregate that is coated with aged binder will likely have no (or reduced) binder absorption, which will decrease the demand for virgin binder.
RAP binder contribution specifications
GDOT started working with the Georgia Asphalt Pavement Association (GAPA) to find ways to improve the durability of high RAP mixes. As stated earlier, originally 100 percent credit was assumed for RAP binder content contribution in mix design specifications. A decision was made to start a step-by-step process of reducing the allowable RAP binder contribution rate starting in 2012.
The first step was to change from 100 percent to 75 percent RAP binder contribution ratio which is used to calculate the Correct Optimum Asphalt Content (COAC) which was referred to as 75:25 COAC.
Seeing definite improvement with the additional binder content but concluding that additional improvement was possible, the second step was to move to 60 percent binder contribution ratio (60:40 COAC) in 2019.
The table showing the calculations that would be used when the RAP binder content is 5.09 percent from ignition oven testing and the 0.60 binder credit ratio is used. A substantial increase in the total binder content and improvement in the ratio of virgin/ RAP binder ratio resulted from the change.
Corrected Optimum Asphalt Content (COAC) (60% RAP Binder Contribution) RAP and Virgin Binder Calculation |
• Total optimum AC in mix design = 4.25% • Percentage of RAP in mix design = 30% • AC in RAP = 5.09% • RAP AC contribution = (5.09 x .30) = 1.53% • Using GDOT 0.60 RAP binder credit ratio • 1.53% x 0.60 = 0.92% • 1.53% – 0.92% = 0.61% • JMF COAC = 4.25 + 0.61 = 4.86% • Virgin AC % = 4.86 – 1.53% = 3.33% |
For this example, 0.61% increase in virgin binder content. All mix design performance testing will be conducted at 4.86% binder content. |
in this example, while a standard volumetric mix design would result in a design binder content of 4.25 percent for a mixture containing 30 percent RAP, the COAC approach (at the 60 percent binder replacement level) would result in a binder content of 4.86 percent (a 0.61 percent increase in total binder content) with the percentage of virgin binder increasing from 2.72 percent to 3.33 percent.
Improvements and benefits
Since the implementation of the COAC specification requirement, more than 200 field verifications using 75:25 COAC and 60:40 COAC were conducted with no issues with production, construction or lab testing.
Improvement in the appearance and uniformity of surface texture was seen with the significant increase in binder content for these mixes. Finally, very few density-related pay reductions occurred on the verification projects.
GDOT plans to monitor the performance of the field verification projects to verify improvement in performance but it is anticipated that there will be an improvement in durability as a result of adopting COAC procedures by GDOT.
“Industry and GDOT were able to work together over the course of a couple of years to make a number of changes to our mixes that improved quality. By far, the change that has moved the needle most has been COAC. Even the contractors that weren’t excited about it in the beginning are proponents now,” said GAPA (Georgia Asphalt Pavement Association) Technical Director Will Rogers.
“The 75:25 COAC mixes have been going down on every paving project for seven or eight years now, and the 60:40 mixes started earlier this season. The differences between COAC and non-COAC mixes are dramatic,” Rogers added.
The bottom line
After seeing significant performance issues with pavements that contain high RAP asphalt mixtures, Georgia DOT’s Office of Materials and Testing made the decision to be proactive in solving the problem. A number of changes have been implemented in the last several years including the adoption of the COAC 60:40 mix design procedure which reduces the RAP binder contribution and increases virgin binder in the mixes as well as increasing total binder content.
The recent changes in Georgia have been successful in significantly increasing total binder contents in plant-produced mixtures that are easier to place uniformly and compact to specification density. Initial verification projects were very successful and indicate that Georgia motorists are likely to enjoy a significant improvement in the performance life of their asphalt roadways.
Horan is an Asphalt Institute Senior Regional Engineer based in Virginia.